Historia Toyotismo, cechy, fazy, zalety i wady
The toyotismo, system produkcji Toyoty (TPS) lub lean manufacturing (produkcja bez odpadów) jeden z trzech głównych modeli systemów produkcyjnych, które powstały w odpowiedzi na szczególne okoliczności towarzyszące firmie Toyota w początkowym okresie.
W tym sensie wiele z jego podstawowych pojęć jest starych i wyłącznie dla Toyoty. Inni mają swoje korzenie w bardziej tradycyjnych źródłach. Zostały one przyjęte jako najlepsze praktyki w wielu innych branżach, poza produkcją samochodową.
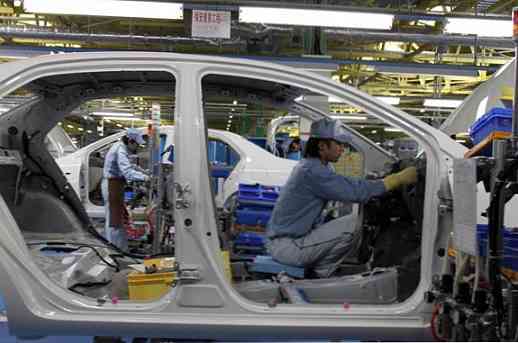
System produkcyjny Toyoty jest wykorzystywany głównie w dużych przedsiębiorstwach skoncentrowanych na produkcji masowej. Jego cechami charakterystycznymi są gospodarka odpadami (lean management) i produkcja bez odpadów (lean manufacturing).
W 1990 r. Dobrze znane badanie przeprowadzone przez Massachusetts Institute of Technology ustaliło czynniki sukcesu Toyoty. Były to przywództwo technologiczne, przywództwo kosztowe i przywództwo czasowe.
Podejście korporacyjne i podstawowa strategia firmy uznają fabrykę za kompletny system. To jest system pracy, który nakłada się na poszczególne stanowiska pracy i warsztat.
Indeks
- 1 Historia
- 2 Charakterystyka toyotismo
- 3 fazy
- 3.1 Projektowanie prostego systemu produkcyjnego
- 3.2 Identyfikacja przestrzeni do ulepszeń
- 3.3 Ciągłe doskonalenie
- 4 zalety
- 4.1 Zmniejszyć ilość odpadów
- 4.2 Poszukaj wydajności
- 4.3 Zmniejszenie kosztów
- 5 Wady
- 5.1 Konieczna jest ocena ulepszeń
- 5.2 Działa lepiej ze stabilnymi komponentami
- 6 Przykłady firm, które używają toyotismo
- 7 referencji
Historia
W 1902 roku Sakichi Toyoda wynalazł krosno, które zatrzymywało się automatycznie, gdy wykrył, że nić pękła. Zapobiegło to tworzeniu wadliwego materiału.
Później, w 1924 r., Stworzył automatyczne krosno, które umożliwiło człowiekowi obsługę wielu maszyn. Takie było źródło jednego z pojęć Toyotizmu: jidoki. Koncepcja ta jest związana z jakością procesu produkcyjnego i oddzieleniem człowieka od maszyny do zarządzania wieloma procesami.
Następnie Sakichi stworzył firmę motoryzacyjną, która pozostała pod opieką Kiichiro Toyody, jego syna. W 1937 roku Kiichiro ukuł frazę w samą porę (w samą porę).
Ze względu na brak wystarczających środków firma nie mogła marnować pieniędzy na nadmiar sprzętu lub materiałów w produkcji. Wszystko musi być na czas, nie za wcześnie ani za późno. Stało się to drugim najważniejszym przykazaniem Toyotyzmu.
Po drugiej wojnie światowej inżynierowi Taiichi Ohno powierzono zadanie poprawy wydajności operacyjnej i zarządzania koncepcjami „just in time” i „jidoka”. Został mianowany kierownikiem warsztatu maszynowego fabryki silników i eksperymentował z wieloma koncepcjami w produkcji w latach 1945-1955.
Jego praca i wysiłek w dużej mierze przyczyniły się do sformułowania tego, co obecnie nazywa się Toyota Production System.
Charakterystyka Toyotyzmu
Jedną z cech Toyotizmu jest produkcja małych partii. Ilość pracy wykonanej na każdym etapie procesu jest podyktowana jedynie zapotrzebowaniem na materiały następnego etapu natychmiastowego. Zmniejsza to koszty utrzymania zapasów i czas dostawy.
Z drugiej strony pracownicy są szkoleni w zespołach. Każdy zespół ma obowiązek i szkolenie do wykonywania wielu specjalistycznych zadań.
Przeprowadzają również czyszczenie i naprawę drobnych urządzeń. Każdy zespół ma lidera, który pracuje jako jeden z nich na linii.
Ponadto pracownicy muszą jak najszybciej wykryć i skorygować wady produktu. Jeśli wady nie da się łatwo naprawić, każdy pracownik może zatrzymać całą linię pociągając za kabel.
Wreszcie dostawcy są traktowani jak partnerzy. Są one szkolone w celu skrócenia czasu przygotowania, zapasów, usterek, awarii maszyn i innych.
Fazy
Projekt prostego systemu produkcyjnego
Przepływ systemu produkcyjnego nie powinien mieć przerw. Można to osiągnąć, gdy następuje szybki przepływ surowca do gotowego produktu.
Człowiek (operator) i maszyna (wyposażenie) muszą być systematycznie równoważone zgodnie z wymaganiami klienta.
Identyfikacja przestrzeni do ulepszeń
Ostatecznym celem jest system, który ma jednolity przepływ materiału przy jednoczesnej maksymalizacji wartości dodanej operatora.
Ciągłe doskonalenie
Istotnym aspektem Toyotism jest elastyczność sprzętu i możliwość dostosowania go do elastyczności produktu. Pozwoli to szybko reagować na wymagania klienta, a jednocześnie być producentem na czas..
Zalety
Zmniejsz ilość odpadów
Jedną z zalet Toyotism jest to, że stara się zminimalizować wszelkie formy odpadów. Obejmuje to wszystko, od wad materiałowych po ergonomię pracownika.
Szukaj skuteczności
Unika się również warunków środowiskowych, które utrudniają wydajność pracy. Pracownicy aktywnie uczestniczą w procesach doskonalenia. To wzmacnia ich poczucie przynależności i zwiększa ich motywację.
Zmniejsz koszty
Z drugiej strony strategia „just-in-time” pozwala na lepsze wykorzystanie zasobów firmy. Pomaga także zwiększyć przepływy pieniężne. Zapotrzebowanie na przechowywanie jest zmniejszone, co zmniejsza koszty.
Zaoszczędzone miejsce w pamięci można wykorzystać do dodania nowych linii produktów. A personel ma więcej czasu na szybką reakcję na zmiany w zapotrzebowaniu klientów.
Wady
Konieczne jest docenienie ulepszeń
Monitorowanie wydajności i odpadów może wpływać na czas produkcji. Wartość ulepszeń musi zostać zbadana. Jeśli wydajność w sekcji jest większa niż w poprzednim etapie, wyniki nie zostały poprawione.
Działa najlepiej ze stabilnymi komponentami
Inną wadą jest to, że zasady just-in-time działają najlepiej ze stabilnymi komponentami systemu. Wszelkie ograniczenia nieuwzględnione w planowaniu potencjalnie zagrażają całemu systemowi.
Przykłady firm korzystających z Toyotism
Klasycznym przykładem firm, które korzystają z tego systemu, jest oczywiście firma Toyota. Filozofia Toyoty sprawiła, że stała się jedną z najważniejszych firm motoryzacyjnych na świecie. Ta koncepcja została powtórzona na całym świecie.
Jedną z firm, która wdrożyła strategie Toyotism, jest John Deere. Ten producent maszyn rolniczych poczynił znaczące inwestycje, aby przekształcić swoją działalność w Iowa w USA w 2003 roku.
Praktyki te pozwoliły mu zidentyfikować działania bez wartości dodanej i wyeliminować je w miarę możliwości.
Referencje
- Haak, R. (2003). Teoria i zarządzanie strategiami zbiorowymi w biznesie międzynarodowym: wpływ globalizacji na japońskie niemieckie kolaboracje biznesowe w Azji. Nowy Jork: Palgrave Macmillan.
- Sztuka Lean. (s / f). Podstawowy podręcznik Toyota Production System. Pobrane 7 lutego 2018 roku z artoflean.com.
- 1000 przedsięwzięć. (s / f). 7 zasad Toyota Production System (TPS). Pobrane 7 lutego 2018 roku z 1000ventures.com.
- Shpak, S. (s / f). Zalety i wady Lean Production. Pobrane 7 lutego 2018 r. Z smallbusiness.chron.com.
- Basak, D.; Haider, T. i Shrivastava, A. K. (2013). Strategiczne kroki do osiągnięcia Lean Manufacturing Systems w nowoczesnym zarządzaniu operacjami. International Journal of Computer Science and Management Studies, Vol. 13, No. 5, pp. 14-17.
- Globalna produkcja (2014, 11 czerwca). Top 10: Lean firmy produkcyjne na świecie. Pobrane 7 lutego 2018 r. Z manufacturingglobal.com.