Przykłady APQP (Advanced Product Quality Planning)
APQP (zaawansowane planowanie jakości produktów), Będąc w hiszpańskim „Zaawansowanym Planowaniu Jakości Produktów”, jest to schemat procedur i technik stosowanych do rozwoju produktów w przemyśle, w szczególności motoryzacyjnym..
Złożone produkty i łańcuchy dostaw stwarzają wiele możliwości awarii, zwłaszcza gdy wprowadzane są nowe produkty. APQP to ustrukturyzowany proces projektowania produktów i procesów, którego celem jest zagwarantowanie zadowolenia klientów z nowych produktów lub procesów.
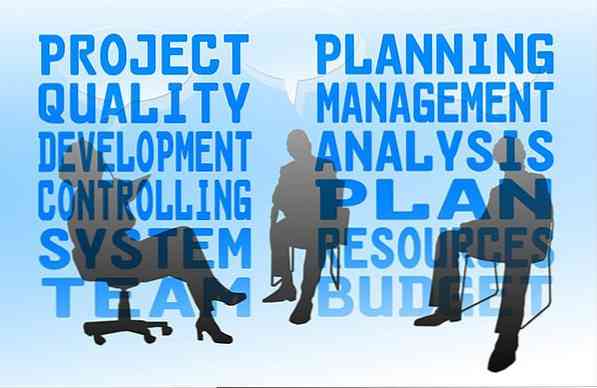
Podejście to wykorzystuje narzędzia i metody, aby zmniejszyć ryzyko związane ze zmianami w nowym produkcie lub procesie.
Jego celem jest opracowanie znormalizowanego planu wymagań jakościowych produktów, który pozwala dostawcom zaprojektować produkt lub usługę, która zadowala klienta, ułatwiając komunikację i współpracę między różnymi działaniami.
W procesie APQP wykorzystywany jest zespół wielofunkcyjny, który obejmuje marketing, projektowanie produktów, zakupy, produkcję i dystrybucję. Proces ten jest wykorzystywany przez General Motors, Ford, Chrysler i jego dostawców do systemu rozwoju produktu.
Indeks
- 1 fazy
- 1.1 Faza 1: Planowanie i definicja programu
- 1.2 Faza 2: Projektowanie i rozwój produktu
- 1.3 Faza 3: Projektowanie i rozwój procesu wytwarzania produktu
- 1.4 Faza 4: Walidacja procesu i produktu
- 1.5 Faza 5: Uruchomienie, oceny i ciągłe doskonalenie
- 2 Przykład
- 2.1 Gdzie włączyć APQP
- 2.2 Branże, które go używają
- 3 referencje
Fazy
APQP służy jako przewodnik w procesie rozwoju, a także jako standardowy sposób udostępniania wyników między dostawcami i firmami motoryzacyjnymi. Składa się z pięciu faz:
Faza 1: Planowanie i definicja programu
Gdy zapotrzebowanie klientów wymaga wprowadzenia nowego produktu lub zmiany istniejącego, planowanie staje się głównym tematem, nawet przed dyskusjami na temat projektu lub przeprojektowania produktu.
W tej fazie planowanie ma na celu zrozumienie potrzeb klienta, a także oczekiwań produktu.
Działania planistyczne obejmują zbieranie danych niezbędnych do określenia, czego klient chce, a następnie wykorzystanie tych informacji do omówienia cech produktu.
Następnie możesz zdefiniować program jakości niezbędny do utworzenia produktu zgodnie ze specyfikacją.
Rezultatem tej pracy jest projektowanie produktu, niezawodność i cele jakościowe.
Faza 2: Projektowanie i rozwój produktu
Celem tej fazy jest ukończenie projektu produktu. W tym miejscu ma miejsce ocena żywotności produktu. Wyniki pracy w tej fazie obejmują:
- Przegląd i weryfikacja ukończonego projektu.
- Zdefiniowane specyfikacje materiałów i wymagań sprzętowych.
- Analiza efektu i trybu awarii ukończonego projektu w celu oceny prawdopodobieństwa awarii.
- Plany kontroli ustanowione dla stworzenia prototypu produktu.
Faza 3: Projektowanie i rozwój procesu wytwarzania produktu
Ta faza koncentruje się na planowaniu procesu produkcyjnego, który będzie produkował nowy lub ulepszony produkt.
Celem jest zaprojektowanie i rozwój procesu produkcji z uwzględnieniem specyfikacji i jakości produktu oraz kosztów produkcji.
Proces musi być w stanie wyprodukować ilości niezbędne do zaspokojenia oczekiwanego popytu konsumentów, przy jednoczesnym zachowaniu wydajności. Wyniki w tej fazie obejmują:
- Kompletna konfiguracja przebiegu procesu.
- Analiza efektu i trybu awarii całego procesu w celu identyfikacji i zarządzania ryzykiem.
- Specyfikacje jakości procesu operacyjnego.
- Wymagania dotyczące opakowania i wykończenia produktu.
Faza 4: Walidacja procesu i produktu
Jest to faza testowania, aby potwierdzić proces produkcyjny i produkt końcowy. Kroki w tej fazie obejmują:
- Potwierdzenie zdolności i niezawodności procesu produkcyjnego. Podobnie, kryterium akceptacji jakości produktu.
- Realizacja testów produkcyjnych.
- Test produktu w celu potwierdzenia skuteczności wdrożonego podejścia produkcyjnego.
- Dokonaj niezbędnych zmian, zanim przejdziesz do następnej fazy.
Faza 5: Uruchomienie, oceny i ciągłe doskonalenie
W tej fazie rozpoczyna się produkcja na dużą skalę, z naciskiem na ocenę i ulepszanie procesów.
Jednym z filarów tej fazy jest zmniejszenie zmienności procesu, identyfikacja problemów, a także inicjowanie działań naprawczych w celu wsparcia ciągłego doskonalenia.
Istnieje również zbieranie i ocena opinii klientów i danych związanych z wydajnością procesów i planowaniem jakości. Wyniki obejmują:
- Lepszy proces produkcyjny poprzez zmniejszenie wahań procesu.
- Poprawa jakości w dostarczaniu produktu i usługi do klienta.
- Poprawa satysfakcji klienta.
Przykład
Gdzie włączyć APQP
- Opracowanie wymagań od głosu klienta, z wykorzystaniem funkcji jakości.
- Opracowanie planu jakości produktu zintegrowanego z harmonogramem projektu.
- Działania projektowe produktu, które przed wydaniem projektu przekazują szczególne cechy lub klucze do czynności projektowania procesu. Obejmuje to nowe kształty i części, dokładniejsze tolerancje i nowe materiały.
- Opracowanie planów testów.
- Wykorzystanie formalnego przeglądu projektu do śledzenia postępów.
- Planowanie, nabywanie i instalacja odpowiedniego sprzętu i narzędzi procesu, zgodnie z tolerancjami projektowymi podanymi przez źródło projektu produktu.
- Przekazywanie sugestii przez personel montażowy i produkcyjny na temat sposobów lepszego montażu produktu.
- Ustanowienie odpowiednich kontroli jakości dla specjalnych cech lub kluczy produktu lub parametrów procesu, które nadal stwarzają ryzyko potencjalnych awarii.
- Realizacja badań stabilności i zdolności specjalnych cech, aby zrozumieć obecną zmienność, a tym samym przewidzieć przyszłe wyniki dzięki statystycznej kontroli procesów i zdolności procesu.
Branże, które go używają
Ford Motor Company opublikował pierwszy zaawansowany podręcznik planowania jakości dla swoich dostawców na początku lat osiemdziesiątych, co pomogło dostawcom Forda opracować odpowiednie mechanizmy zapobiegania i wykrywania nowych produktów, wspierając w ten sposób wysiłek firmy.
Pod koniec lat 80. główni producenci przemysłu motoryzacyjnego korzystali z programów APQP. General Motors, Ford i Chrysler wdrożyły i dostrzegły potrzebę zjednoczenia się, aby stworzyć dla swoich dostawców wspólny rdzeń zasad planowania jakości produktów.
Wytyczne zostały ustanowione na początku lat 90-tych, aby zapewnić przestrzeganie protokołów APQP w znormalizowanym formacie.
Przedstawiciele trzech producentów motoryzacyjnych i Amerykańskiego Towarzystwa Kontroli Jakości stworzyli grupę wymagań jakościowych, aby mieć wspólne zrozumienie tematów będących przedmiotem wspólnego zainteresowania w przemyśle motoryzacyjnym..
Metodologia ta jest obecnie wykorzystywana przez firmy progresywne, aby zagwarantować jakość i wydajność poprzez planowanie.
Referencje
- Wikipedia, darmowa encyklopedia (2018). Zaawansowane planowanie jakości produktów. Zrobiono z: en.wikipedia.org.
- NPD Solutions (2018). Zaawansowane planowanie jakości produktów. Zaczerpnięte z: npd-solutions.com.
- Quality-One (2018). Zaawansowane planowanie jakości produktu (APQP). Zrobione z: quality-one.com.
- Przynęty (2018). 5 faz APQP: przegląd kluczowych wymagań. Zrobiono z: cebos.com.
- David Ingram (2018). Zaawansowane planowanie jakości produktów. Small Business - Chron.com. Zrobiono z: smallbusiness.chron.com.